Concrete blocks are the foundations of the modern world but they could be greener. Tom Heap meets Professor Colin Hills and his team turning waste dust and carbon dioxide into building materials.
Professor Hills, of the University of Greenwich, has developed a technique that mimics natural processes, using carbon dioxide as a glue to form stone aggregates from waste dust left behind by heavy industry. The spin-off company, Carbon 8 Systems, has compressed the process into a shipping container and now makes building materials in the UK and France with this clever carbon-munching technique. Colin's colleague, Nimisha Tripathi wants to adapt the system for the developing world, choosing waste from her native India - things like pistachio shells and banana skin - to make a tailored range of building products relevant to the region in which they're made.
What our experts say
We asked Society Fellows Dr Rupert Myers and Professor Paul Fennell from Imperial College London, and Professor Karen Scrivener from École Polytechnique Fédérale de Lausanne to offer some observations on the potential of using low carbon cement as a building material in reducing carbon emissions. Their points take some of the themes of the programme a step further.
What are the limiting factors?
Dr Rupert Myers
The main limitation for carbonated aggregates is the availability of carbonatable feedstocks. They need to contain calcium oxide (CaO) or magnesium oxide (MgO) and are thus usually by-products from high temperature industrial processes, e.g. fly ashes, iron and steel slags, cement kiln dusts. Igneous rocks like olivine and basalt can also be used but anthropogenic feedstocks provide an economic incentive through waste treatment/landfill diversion. The use of carbon8 systems (c8s)-type (accelerated carbonation) technology on igneous rocks is a massively scalable form of carbon dioxide (CO2) sequestration. However, it does not have technical advantages over using the virgin aggregate directly, so is only economically feasible if the price of CO2 emissions is high enough.
Competition for some of the most highly available anthropogenic feedstocks poses a challenge to expand application of c8s technology to these materials - coal fly ashes and blast furnace slag. Good quality coal fly ashes and blast furnace slags are cementitious and are currently used to replace Portland cement clinker in cement. It is also better to avoid Portland cement clinker production (which is more CO2 emissions intense) than to produce aggregates.
Lightweight aggregates produced by c8s are not suitable for all aggregate applications e.g. some types of concrete require normal (dense) aggregate. But, as there is lots of CO2 containing flue gas available, this isn’t a limitation (>10 Gt/year from point sources only).
In general, the limiting factors of decarbonisation measures for cementitious materials are:
-
Standards. International Organization for Standardization (ISO) standards prescribe (limited) ranges of cement constituents (EN 197-1) rather than specify cementitious product performance, which limits materials innovation.
-
Cost. Cement is a relatively low value product. This makes it difficult to implement relatively expensive decarbonisation measures like carbon capture and storage, since that would significantly increase the price of cement.
-
Global scale. Cement raw materials (limestone, siliceous rocks) are available in abundance nearly everywhere (relative to large human populations). There are relatively few other materials that meet this criterion.
-
Chemistry. Conventional cements require CaO, which is sourced from limestone (CaCO3). Significantly different material chemistries (e.g., sigma-aldrich (SiO2-Al2O3)) are needed to approach complete Portland cement clinker substitution. This increases risk/expense (by needing additional testing and expertise to prove performance) and can undermine ISO compliance.
-
Ease of use. 'Just add water'. Non-hazardous. Centuries of experience with Portland cement.
-
Timber availability is limited. We would need to massively upscale timber supply (e.g. doubling or greater) for substantial timber for concrete substitution globally.
Professor Paul Fennell
-
There are alternative uses for some of the materials that are used to produce the final products, and some of them lead to lower CO2 overall than producing aggregates in this manner.
-
Carbon8 does not produce cement, it produces aggregates that go into cement. They bulk up the cement, and the cement glues them together. The aggregates that carbon8 produce are replacements for gravel and sand in concrete, not cement.
-
If you are looking for low carbon cement, you need to go to Solidia or other technologies, but they are not really structural cement, which is about 70% of the market. For structural cement we will likely need to go to carbon capture and storage on a cement plant.
Professor Karen Scrivener
-
Fly ash comes from burning coal to produce electricity. There is a lot of pressure to phase out coal fired power production as this is the major contributor to CO2. The annual amount of fly ash currently available worldwide is about 25% of cement production. About one third of this amount is already used as a component of cement or concrete, which means it is already contributing to CO2 reduction.
-
The carbon8 technology relies on the CaO component of the fly ash reacting with CO2 to produce calcium carbonate. This calcium carbonate is then used as a substitute for normal aggregate, but the strength of the calcium carbonate produced is much lower than most normal aggregates, so it is really unclear if there is really any CO2 reduction in the final concrete. Not least such substandard aggregate needs to be accepted in codes and standards which would really slow down the use at scale.
-
Even assuming a best case scenario, I estimate the maximum CO2 reduction possible from this technology to be less than 50 million tonnes of CO2 per year. This is less than one tenth of what can be achieved by other low carbon cement technologies, such as LC3. This figure is an estimate from the production of fly ash today and it must be considered that this is going down in many countries, particularly Europe.
-
The technology is quite complex in terms of equipment and logistics. It would be very unlikely to be adopted in developing countries where the demand for cement is growing fastest. For example, Europe uses only around 5% of current cement production.
-
Sources of uncarbonated CaO, such as in fly ash, can already be used as feedstock for cement production, this way the CO2 savings can be simply realised without the need for any new installation.
What are the co-benefits?
Dr Rupert Myers
-
Otherwise difficult to utilise wastes can be valorised (e.g. air pollution control residues (APCr)).
-
Reduces landfilling.
-
Carbonation can improve material properties.
-
Carbonation can bind various heavy metals that would otherwise be more mobile in the waste feedstocks.
Decarbonisation measures for cementitious materials (in general):
-
Valuable use of industrial by-products, as raw materials e.g. coal fly ash, and wastes as kiln fuels that have limited alternative applications e.g. used car tyres.
-
Reduces landfilling.
-
Can continue to use mortar and concrete, which are hugely popular and commonly used materials worldwide.
-
Uses less land than timber (since quarries are three dimensional), and good quality land is a scarce resource (and will increasingly become so due to urbanisation and population growth [means more demand for food]).
Professor Paul Fennell
In the case of carbon8, waste remediation is the main one. By carbonating the wastes, they prevent mobility of any trace elements that are present.
Are there any potential negative impacts of this idea?
Dr Rupert Myers
There are no major potential negative impacts for c8s.
Decarbonisation measures for cementitious materials (in general):
-
Carbon capture and storage and other measures that increase material cost (kiln electrification, use of hydrogen as fuel?). In developing countries there is more informal construction than in developed countries. Materials represent a larger share of costs in informal construction than in industrialised construction. So, implementing expensive measures can disproportionally make construction more expensive in developing countries.
-
It is more challenging to verify the performance of less conventional materials due to lesser history of use. Ultimately, I expect this will increase material and/or design and/or construction cost. But this will be somewhat overcome by manufacturing components off-site since concrete curing can be better controlled in those environments.
Professor Paul Fennell
-
The manufactured aggregates are a bit more expensive than regular aggregates.
-
The cement itself, that glues the aggregates together, produces around 500kg of CO2 per tonne, and that also needs decarbonising.
-
These 'new' aggregates resemble secondary aggregates, which can only be used in a relatively small number of applications.
Professor Karen Scrivener
-
Poor quality concrete due to low strength of aggregates.
It is very important that we do move to low carbon cement, but this technology is unlikely to be the best way to do it.
Further reading
Favier, A., et al. (2018) A sustainable future for the European Cement and Concrete Industry: Technology assessment for full decarbonisation of the industry by 2050, ETH Zurich
Fennell, P.S., Davis, S. and Mohammed, A. (2021) Decarbonizing cement production, Joule, 1305-1311
Gunning, P. et al (2011) Novel approaches to the valorisation of ashes using aggregation by carbonation, Proceedings of the Second International Slag Valorisation Symposium, 2011
Gunning, P., and Hills, C.D. (2014) Carbon negative first commercial application of accelerated carbonation technology, Greenwich Academic Literature Archive
Hertwich, E. et al. (2020) Resource Efficiency and Climate Change, International Resource Panel, United Nations Environment Programme, Nairobi, Kenya
Fennell, Davis, Mohammed, 16 June 2021. Joule Vol 5, Issue 6, 1305-1311
Pamenter, S.K., and Myers, R.J. (2021) Decarbonizing the cementitious materials cycle: A whole-systems review of measures to decarbonize the cement supply chain in the UK and European contexts, Journal of Industrial Ecology, 25, 359–376,
Scrivener, K. et al. (2018) Calcined clay limestone cements (LC3), Cement and Concrete Research, 114, 49-56
Scrivener, K. (2020) A concrete idea to reduce carbon emissions, TED
UNEP (2017) Eco-efficient cements: Potential economically viable solutions for a low-CO2 cement-based materials industry
About the series
39 Ways to Save the Planet is a new radio series by BBC Radio 4 developed in partnership with the Society and broadcast in 2021. It showcases 39 ideas to relieve the stress that climate change is placing on the Earth. In each 15 minute episode Tom Heap and Dr Tamsin Edwards meet the people behind a fresh and fascinating idea to cut the carbon.
Over the course of 2021, the Society will be producing events and digital content to accompany the series.
Episode 28: Better bricks
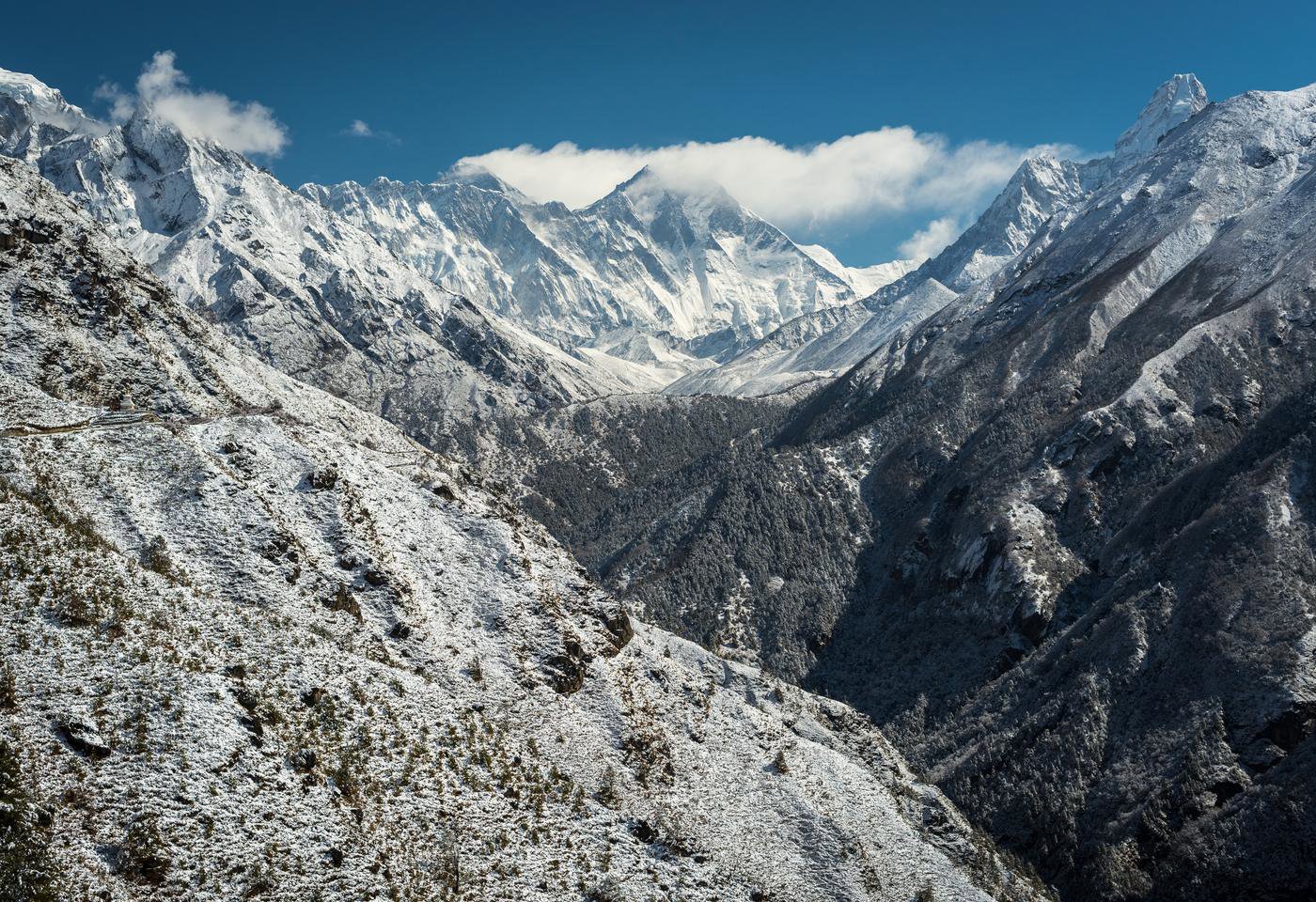
Featured card image: BBC
Featured banner image: PerfectLazybones/AdobeStock
We’ve recently calculated a very rough figure of 4 metric tonnes per year (Mt/yr) of CO2 possible for this technology in the EU (for the most sensible applications) but the costs would be quite high for mitigation. I can’t see much more than 80 Mt/yr for the planet, as a whole, given that.